Over the past few months there have been a lot of rumors and fears swirling online about Fort Mill’s Silfab Solar facility.
In an interview with WCNC, Silfab COO Treff MacDonald attempted to combat some of those claims, saing, ‘there is no smokestack’, the chemicals they use are ‘generally there in the environment’, and that the only thing they will pump into the air is ‘water vapor’. He argued that they do not need to be rezoned to ‘heavy industrial’ since they are only “assembling” solar panels, not “manufacturing” them.
To find out the truth, our team dug through hundreds of Silfab documents, combed through South Carolina DHEC reports, talked to industry experts, and researched similar facilities around the world to find out what’s really being planned in the heart of Fort Mill.
Here’s what we found:
Will there be a 70-foot-tall ‘smoke stack’?
No, but DHEC is requiring that Silfab build a 70-foot-tall ‘acid scrubber stack’ to treat the airborne chemicals used at the facility. While this looks similar to a ‘smoke stack’, the air that will come out of the top will be 96% clean (when the stack is brand new). The remaining 4% will contain a cocktail of Class 3 and other pollutants, including; Hydrogen Fluoride, Silicone Tetrafluoride, and a variety of other VOCs (volatile organic compounds). The air coming out of the stack will exit at a rate of 90 feet per second and will operate 24/7.
According to DHEC’s 1,500 meter modeling analysis, approximately 100 tons of VOC pollutants will be pumped into the air each year from the Silfab facility (this does not include the additional chemicals and VOCs that travel outside of the 1,500 meter analysis zone).
Will Silfab use dangerous chemicals?
Silfab claims the chemicals they will use are ‘generally there in the environment’ and people are only scared of them because of their ‘trade name’.
Page 4 of DHEC’s permit states, “It has been determined that this facility is subject to S.C. Regulation 61-62.68, Chemical Accident Prevention Provisions, due to in-process storage or use of a regulated substance in quantities above the specified threshold.”
According to DHEC, Silfab will store; 15,850 gallons of Hydrofluoric Acid on site in two tanks, 22,983 pounds of Silane in one tank, and will use 132 gallons of Toluene per year.
Silane is potentially the most dangerous. According to the National Oceanic and Atmospheric Administration (NOAA), Silane “ignites spontaneously in air at room temperature”. In the case of any Silane accident, NOAA recommends “initial evacuation for 1600 meters (1 mile) in all directions”.
The vast majority of factories that use Silane have it directly piped in to avoid explosions on the highway or when it is transferred from the truck to the on-site storage tank. Silfab plans on having their Silane trucked in at regular intervals using I-77 rather than having it piped in directly.
Will it be an “assembly facility” or a “factory”?
According to a Silfab press release dated May 20th, “Silfab’s newest factory in South Carolina will soon add 1 gigawatt American-made cell production and another 1.3 gigawatts of module production.”
Silfab states their ‘factory’ will “interconnect solar cells through a conductive medium”. This process is scientifically called ‘close-space sublimation’, a chemical process which enamels cells together. Silfab will use over 1 million gallons of water per day in this enameling process and then treat that water before discharge.
Will it be “light industrial” or “heavy industrial”?
Silfab’s Fort Mill facility at 7149 Logistics Lane is currently zoned LI or “Light Industrial”.
According to the YORK COUNTY CODE OF ORDINANCES CHAPTER 155: ZONING CODE, “LIGHT INDUSTRIAL does not include hazardous material treatment and storage facilities, plating or enameling, or petroleum and gas refining”.
As this article has already stated, the Fort Mill Silfab facility will both treat and store hazardous materials and will engage in an ongoing enameling processes, clearly violating York County’s Light Industrial zoning code.
Silfab has also recently hired SPG to help set up their factory. According to SPG.net, the company is “focused solely on process and heavy industrial capital projects”.
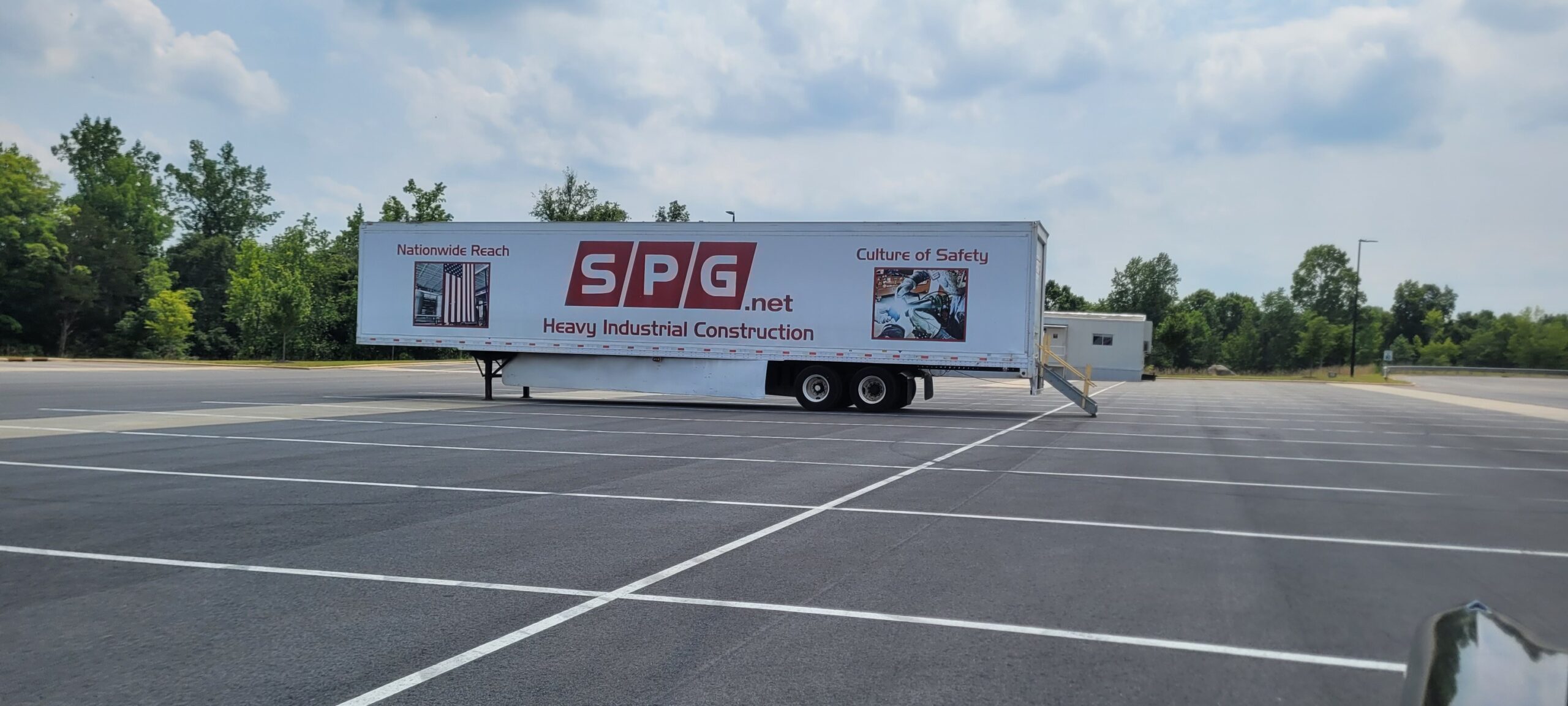
Will Silfab do more than just manufacture panels?
There have been some rumors that once their factory is up and running, Silfab will start recycling used panels.
According to SilfabSolarSC.com, “We are constantly improving our sustainability efforts by investing in new technology, refurbishing old panels, recycling unused products”
Silfab also has a job listing on their website for a full-time “Environmental Engineer” including the following “Essential Duties and Responsibilities”:
- Improving environmental conservation management, including recycling, public health, and water and air pollution
- Undertaking environment protection projects such as designing air pollution management system
- Investigate, record, and compile reports for environmental-related complaints, pollution-control, and waste treatment planning
- Develop guidelines for the disposal of hazardous materials
According to TheChemicalEngineer.com, “Currently, management of solar panel waste generally involves removal of the frame – which can be reused or downcycled – before the remaining components are crushed and landfilled. Excluding the frame and junction box, solar panels are typically comprised of solar cells sandwiched between front glass and a back sheet, with layers of the encapsulant ethylene vinyl acetate (EVA) between. Those exploring recovery begin by separating these layers before crushing up the cells into powder and using chemical leaching to recover reuseable materials.”
How big will the Silfab facility be?
Sifab states their Fort Mill factory will output “1 gigawatt American-made cell production and another 1.3 gigawatts of module production”. The Fort Mill facility is 785,000-square-foot in size (an average US grocery store is 40,000 square feet in size).
Their Burlington, Washington facility has an annual production output of 400 megawatts of solar panels, given that Silfab panels output about 400 watts per panel, that means they produce about 1 million panels per year in Burlington. 1 gigawatt of cell production and another 1.3 gigawatt of module production means the Fort Mill facility will be producing over 5 million panels each year. The total number of panels they will have to dispose of or recycle is unknown.
What do you think about Silfab’s Fort Mill facility?
If you have any additional questions, concerns, corrections, or additions regarding the above article, feel free to leave a comment below or send us a message using the ‘Contact Us’ link above.